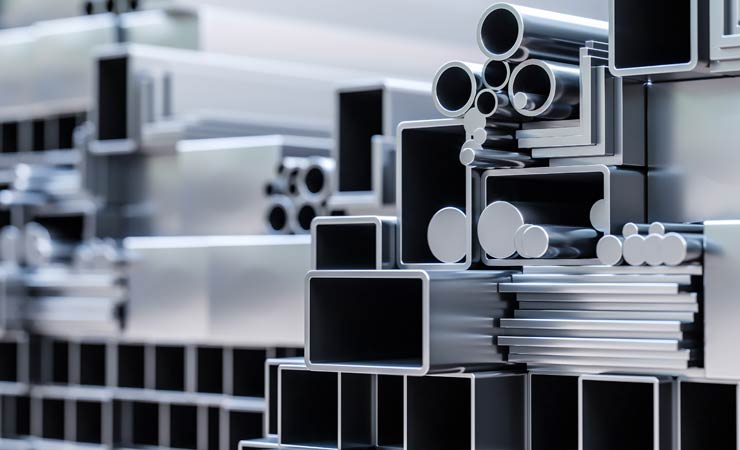
Steel is a versatile and important material that plays a central role in many areas of technology and everyday life. The properties and areas of application of steel are largely determined by its composition and the various alloying elements.
This article shows the most important steel groups and the influence of different alloys.
Basic classification of steel groups
High-quality steel can be divided into different groups based on their chemical composition and mechanical properties. The basic steel groups can be divided into:
- Unalloyed steels: In addition to iron and carbon, these steels contain only a small amount of other elements. They are typically inexpensive and are used for a variety of applications, such as construction and the automotive industry.
- Low-alloy steels: This group of steel contains small amounts of alloying elements such as chromium, nickel or molybdenum and at the same time strengthens various properties such as strength and corrosion resistance.
- High-alloy steels: These steels have a significantly higher proportion of alloying elements and offer special properties such as increased corrosion resistance or heat resistance, which are used in specialized applications.
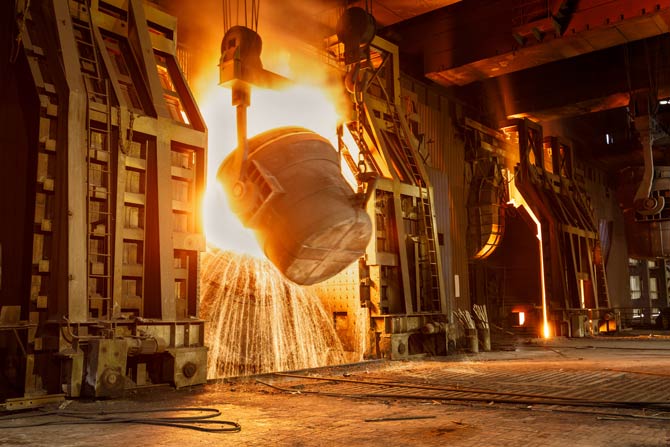
Influence of alloying elements
The addition of alloying elements to steel changes its properties in many ways:
- Aluminium (Al): Aluminum in particular acts as a deoxidizer, which helps calm the casting of steel. Aluminum and nitrogen produce nitrides, which increase the scale resistance and coercivity of steel. When high-alloy steels are combined with aluminum, this has a ferrite-stabilizing effect.
- Beryllium (Be): Beryllium limits the austenite range in iron alloys and acts as a strong deoxidizer in steelmaking. It increases precipitation hardening but can reduce the toughness of iron.
- Bor (B): As an alloying element in iron, boron serves as a strong neutron absorber, which is why steels containing boron are often used in nuclear power plant construction. In addition, boron increases the yield strength and strength of steel, which in turn can reduce corrosion resistance and cause embrittlement in spheroidal graphite cast iron.
- Cerium (Ce): Acts as a deoxidizer in iron. Not only does the scale resistance increase, but spheroidal graphite is also formed. Iron alloys that contain high levels of cerium are pyrophoric, which means they ignite easily when exposed to air.
- Chrom (Cr): Commonly used in stainless steels and increases the corrosion and oxidation resistance of steel.
- Carbon (C): Carbon is an essential alloying element in steel, which significantly influences its hardness and strength. However, higher carbon content reduces machinability and weldability. The carbon content is adjusted depending on the intended use of the steel. When combined with elements such as chromium, vanadium and tungsten, carbon forms carbides that increase wear resistance.
- Kupfer (Cu): With the help of copper, the weather resistance and strength of iron alloys is refined. However, this can also reduce the elongation at break.
- Manganese (Mn): Refines the forgeability and weldability as well as the strength and wear resistance of steel. It reduces the tendency to red fracture and shifts certain points in the iron-carbon diagram, which influences the properties of the steel. If you look at manganese in high-alloy steels, it has a ferrite-stabilizing effect.
- Nickel (Ni): With the help of nickel, not only the toughness but also the corrosion resistance is improved. Nickel steels are often used for high quality stainless steel applications.
- Molybdenum (Mo): Increases strength and heat resistance. Often used in tool steels and high performance alloys.
- Phosphor (P): With the help of phosphorus, the tensile strength as well as the hardness and corrosion resistance of iron alloys are increased. However, this also leads to embrittlement.
- Sulfur (S): Sulfur improves the machinability of ferrous alloys but reduces ductility.
- Silicon (Si): As a solid solution hardener, silicon not only increases scale resistance, but also limits the formation of carbides and makes the steel melt less viscous. It increases tensile strength, yield strength and scale resistance and shifts certain points in the iron-carbon diagram.
- Turn (On): Titanium in iron alloys prevents intergranular corrosion by forming titanium carbide (TiC).
- Vanadium (V): As an alloying element, vanadium carbide forms in interaction with carbon and steel, which leads to an increase in strength, wear resistance and toughness. The addition of vanadium creates fine grains in the steel structure, which improves the weldability of these types of steel.
- Wolfram (W): When making steel, tungsten reacts with carbon to form tungsten carbide, giving the steel high hardness and toughness. However, tungsten negatively affects the scale resistance of the steel.
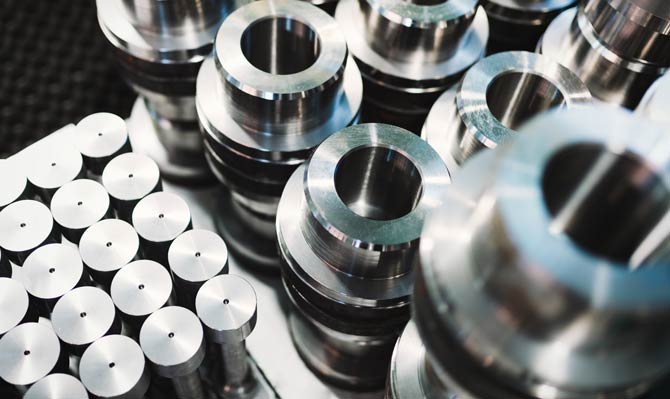
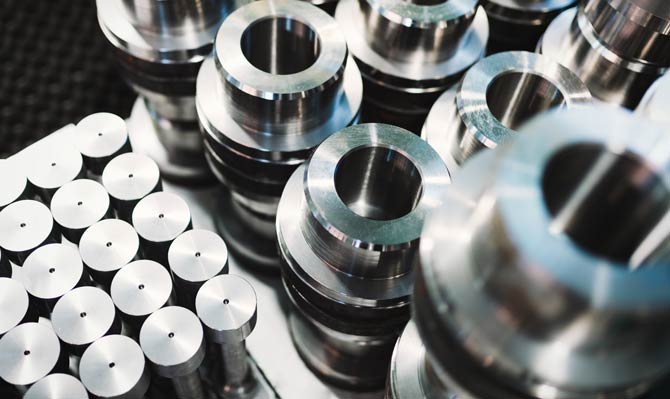
Specific applications and selection of steel alloys
Choosing the right steel alloy depends heavily on the specific application:
- Construction and infrastructure: Unalloyed or low-alloy steels are often used here because they offer a good combination of strength, weldability and cost.
- Tool and Mold Making: High-alloy tool steels containing elements such as chromium, molybdenum and vanadium are common here. They offer high wear resistance and can withstand high loads.
- Automotive industry: The automotive industry requires steels that are light yet high-strength to increase safety and reduce weight. Advanced high-strength steels are often used here.
- Energy production and petrochemicals: These industries often use high-alloy steels that are resistant to extreme temperatures and corrosive environments.
Conclusion: steel groups and the influence of different alloys
In summary, the world of steel is extremely diverse. The different steel groups and alloys offer a wide range of properties that can be tailored to a wide variety of applications.
By understanding the specific properties and effects of alloying elements, the right steel can be found for every requirement.
Source: https://blogg.de/stahlgruppen-und-einfluss-verschiedener-legierungen/