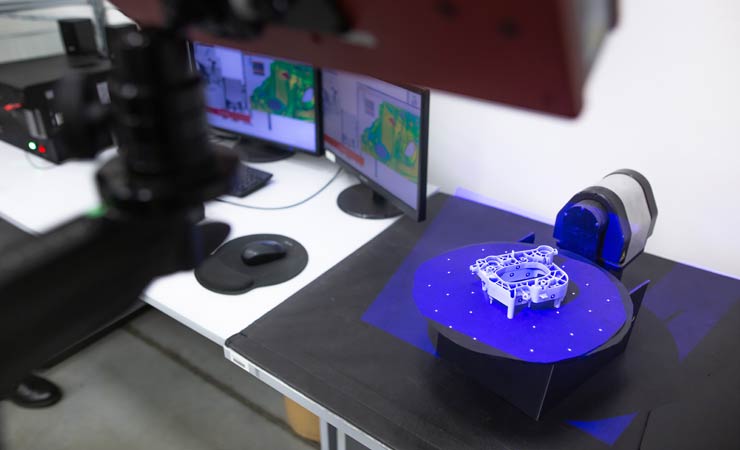
3D scanning with advanced 3D scanners enables the precise optical digitization of real objects – and represents an efficient complement to industrial 3D printing. In 3D scanning, any physical geometry can be converted into high-resolution digital data that can be immediately used for 3D printing. Printing can be used. The process not only offers significant time savings by eliminating manual modeling, but also improves the accuracy and quality of printed products.
This is particularly beneficial in areas such as architecture, medicine and design where precise replicas are required. Additionally, 3D scanning opens up new opportunities for creative customization and iteration as digital models can be easily modified and improved before they are printed.
How 3D scanning works and the process
With 3D scanning, real, physical objects are captured by optical measuring systems and converted into digital data. For the process, which is equally suitable for the smallest components of just a few millimeters in size as well as for large components up to several meters, the objects are first cleaned, degreased and equipped with so-called reference markers.
These markers are used to define the exact coordinates in different object areas for the 3D scanning system.
Light patterns, typically in the form of stripes, are then projected onto the object by a projector. The cameras integrated into the measuring system record how these light patterns are reflected and distorted by the surface of the object. The distortions of the stripes provide information about the 3D shape of the object. Software then calculates the position of each captured point in space from the intersection of the lines of sight of the camera and projector.
The process, known as fringe projection, is considered the most precise technology for optical 3D digitization and is very fast compared to other 3D scanning methods and is suitable for a wide range of materials and surfaces.
The data obtained is provided in the form of STL files. These files describe the surface of the scanned object with triangular polygons and are the preferred format for most 3D printers. In most cases, the STL files are optimized before the actual 3D printing to improve the quality of the 3D printing. Optimization can include adjusting resolution, eliminating geometry errors, or preparing data for specific printing technologies.
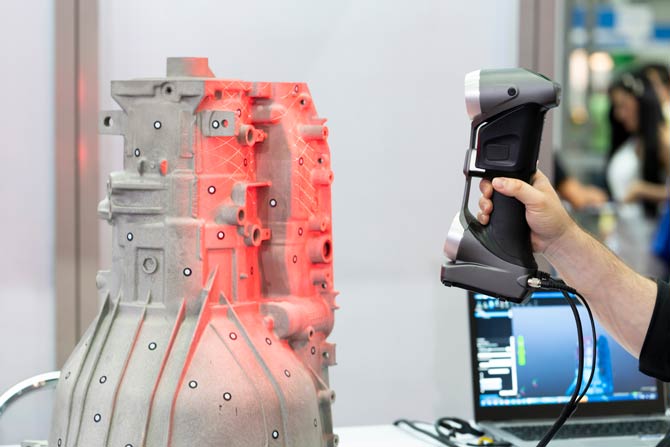
How does 3D scanning complement the 3D printing process?
The 3D scan is used in particular to improve the quality of 3D prints. By capturing the geometric data of a physical object, precise, high-resolution data sets can be generated – which are important for the accuracy of the 3D printed end product.
The data obtained can be checked for errors or dimensional deviations using software, which eliminates time-consuming and therefore expensive misprints. A high-quality 3D scan also complements the printing process perfectly in 3D printing preparation. Since the generated STL files come directly from the scan, they can be used in the 3D printing process without additional conversion steps. This saves time and resources that would otherwise be needed for manually creating digital 3D models.
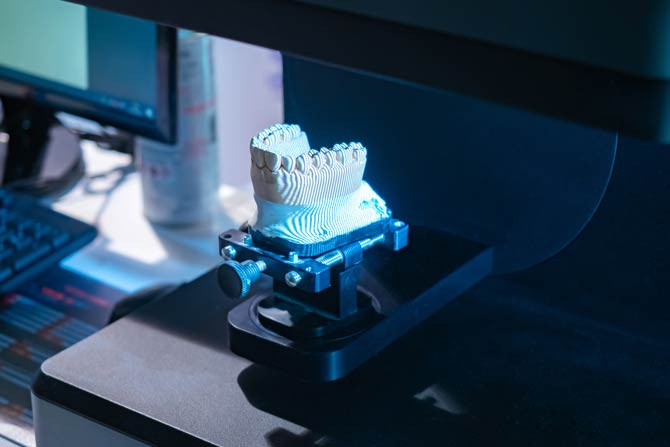
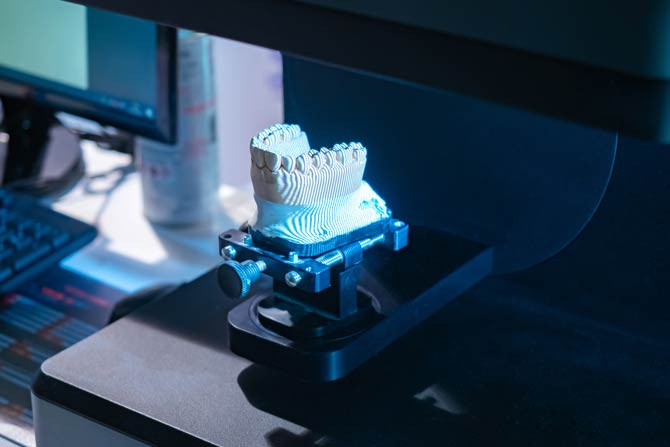
The advantages of a 3D scan for 3D printing:
- Time saving: Using STL data obtained directly from the scan speeds up the entire process from conception to printing.
- Cost efficiency: Because no additional steps are required to convert to CAD data, costs and labor are reduced.
- Attention to detail: 3D scans capture the finest details and complex geometries that can be transferred to 3D printing.
- Customization and modification: The scanned data can be easily modified to make adjustments or design changes before printing.
- Prototyping and iteration: 3D scan data enables particularly fast iterations in the prototyping process.
The 3D scanning service as a service
Whether rapid prototyping, spare parts production or quality assurance: 3D scanning shortens the time from conception to 3D printing – regardless of the size, shape or material of the objects to be scanned. Companies that do not have their own equipment or would like to expand their capacities during peak order times can rely on external, specialized service providers for 3D scanning.
The external support not only offers access to highly developed scanning technologies, but also to expert knowledge in data preparation and optimization for 3D printing. This means companies can access a comprehensive range of services, ranging from the optical capture of a wide range of component sizes to print-ready file preparation. In addition, collaboration with specialized service providers enables flexible scalability of production capacities without the need for invested capital to purchase and maintain expensive equipment. This opens up the opportunity for companies to respond agilely to market requirements and accelerate their development cycles by drawing on the expertise and resources of external partners.
Source: https://blogg.de/3d-scan-effiziente-ergaenzung-fuer-3d-druck/